Chemical
Composition |
C |
Si |
Mn |
Cr |
P |
S |
Mo |
V |
W |
0.40-0.55 |
0.15-1.20 |
0.10-0.40 |
1.00-1.80 |
0.03MAX |
0.03MAX |
0.50 MAX |
0.15-0.30 |
|
1.50-3.00 |
Available
size |
Round Bar |
Diameter |
Length |
16-800mm |
2000-6000mm |
Flat Bar |
Thickness |
Width |
Length |
16-400mm |
100-800mm |
2000-6000mm |
Surface
condition |
Black surface/ Grinded/ Machined |
Annealed
hardness |
HB212MAX |
Characteristics |
AISI S1 is a versatile chrome-tungsten shock-resisting tool steel. Its properties provide excellent service in both cold and hot work shock applications. In addition, it is widely used for master hobs.
It's low carbon content provides toughness and its combination of alloying elements provides the carbide formation necessary for abrasion resistance, the hardenability necessary for shock tools, and improved hot work characteristics.
For additional wear resistance, tools of SI may be carburized during pack hardening. |
Applications |
Heavy duty blanking and forming dies, punches, chisels, shear blades, slitter knives, cold
striking dies, cold extrusion tools, coining dies, master hobs.
Hot work applications with operating temperatures under 1050F such as headers, piercers, forming tools, shear blades, and drop forge die inserts. |
Heat
Treatment |
S1 can be softened to proper structure for machining by heating slowly to 1450 to 1500°F, holding at temperature for at least one hour per inch of greatest thickness, and cooling slowly to 1000°F, after which it may be air- cooled. Hardness resulting from this treatment will be Brinell 212 max. To prevent decarburization, pack or pipe-anneal in sealed containers, using inert material or use a controlled atmosphere furnace. |
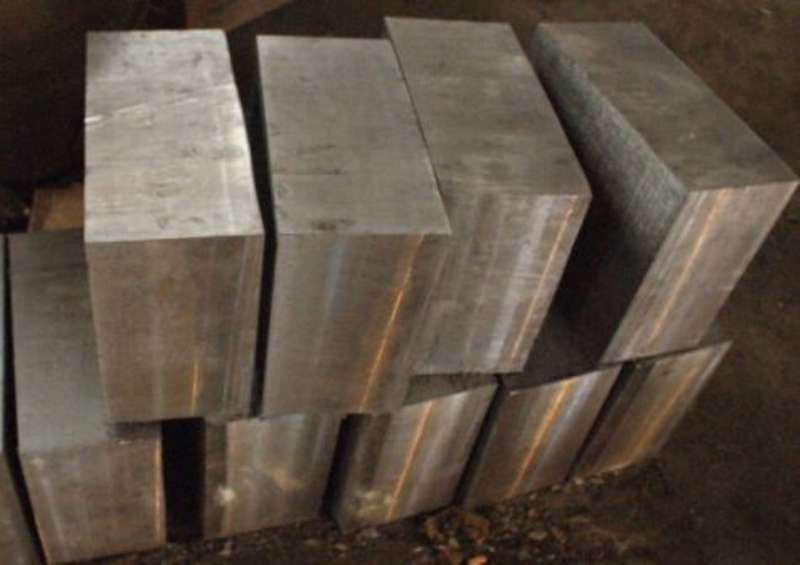
|
|